Royal Arts
Mono Carton Leaflet Insert Mini Outsert
Mono Carton Leaflet Insert Mini Outsert
Unlock the Potential of Your Product With Our Artwork
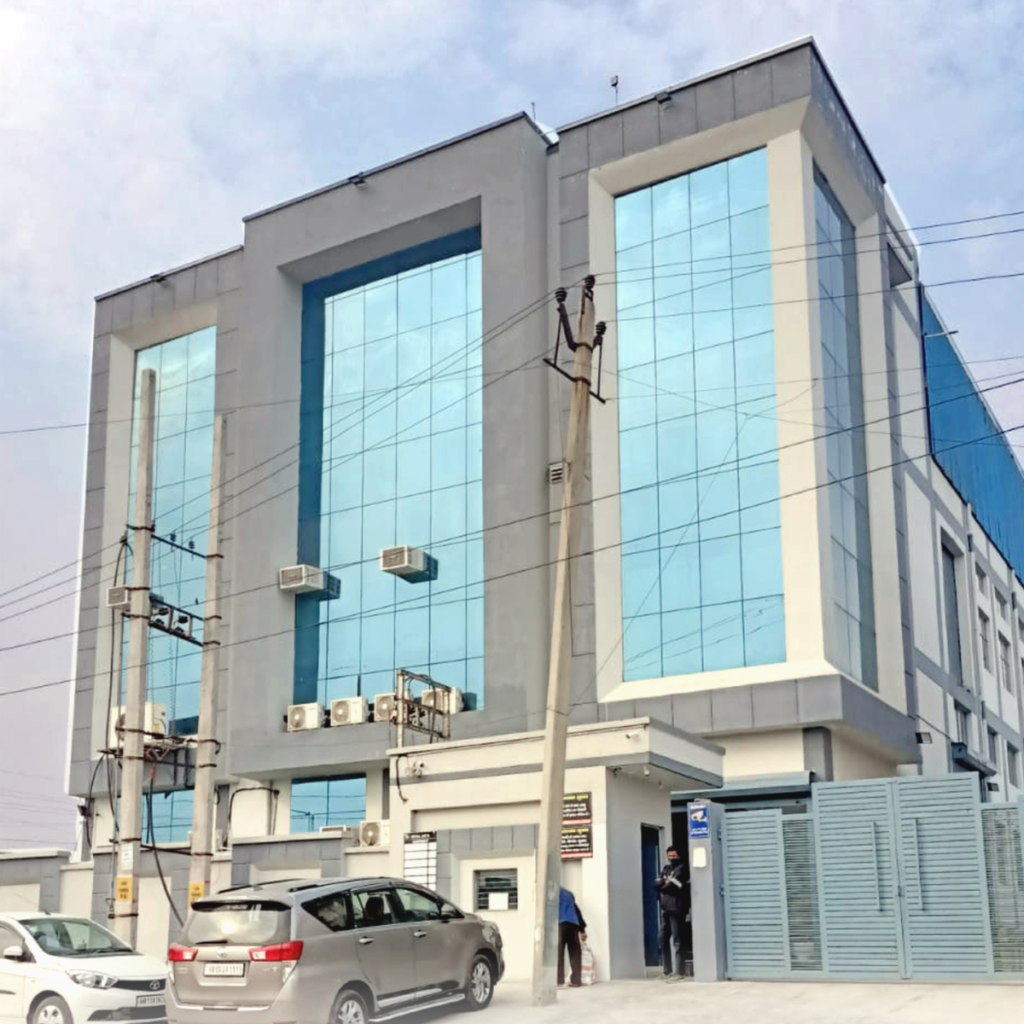
Royal Arts
Royal Arts established in 2014 offers excellent printing and packaging solutions with its state of art in house manufacturing and printing plant
people
9001:2015
Our Vision
Our Mission
our actions.
Our Product Service
We Aim To Providing Best Service To Our Clients Whether It Is Quality Or
Pleasing Customer With The Output They Want We Deal In Almost Every Type Of Offset Related Products For Example Cartons , Leaflets , Outserts , Brochures , Promotional , Materials Bandrolles Ets.
We Have Wonderful Machin To
Do Accurate Braille On Cartons For
Blind People.
We Provide SPOT UV Effect On The Cartons Help To Enhance The Appearance Of The Product.
We Provide Leafing & Dripp Off Effects To Enhance The Appearance Of The Product.
The Only Way To Do Great Work Is ToLove What You Do
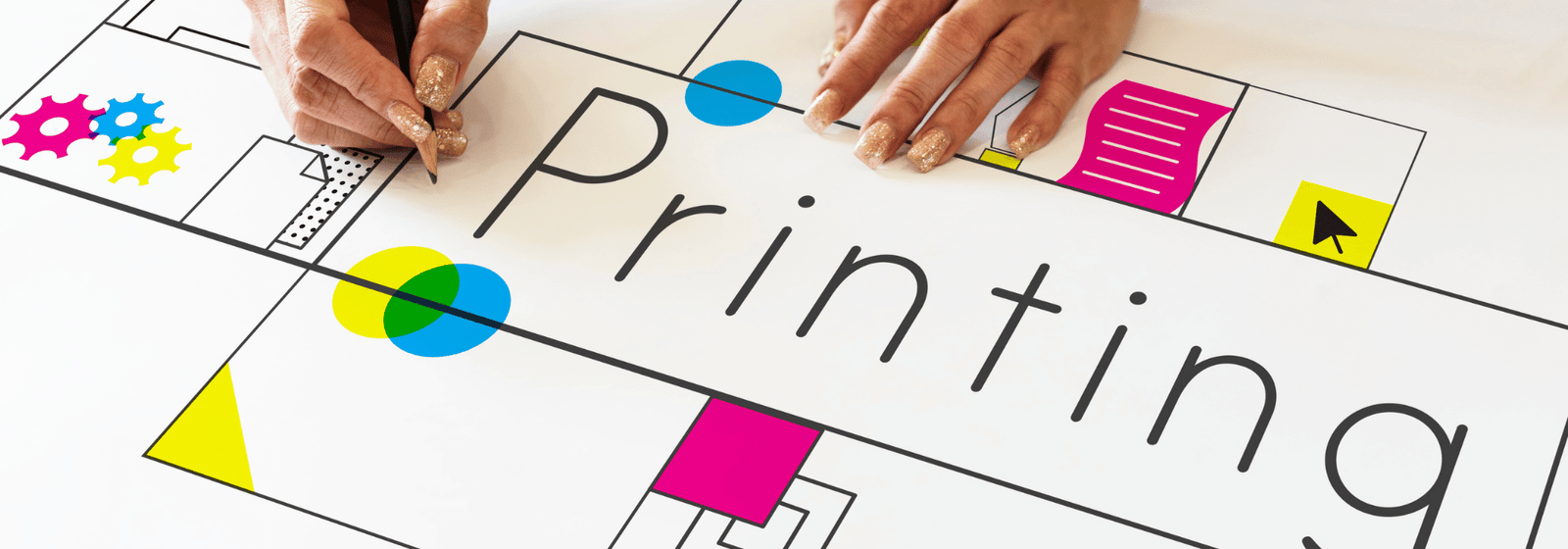
Our Working Process
-
  LEAFLETS PRODUCTION PROCESS 
-
    IN-PROCESS QUALITY CONTROL 
-
CARTON’S PRODUCTION PROCESS
The Production Process Flow in Leaflet for offset packaging involves several key stages to ensure the efficient and effective creation of high-quality packaging materials. Here's a step-by-step overview of the typical process:
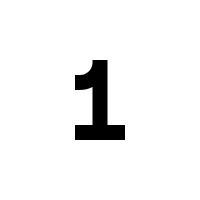
PRE-PRESS PREPARATION
Collaborate with graphic designers or a design team to develop the layout, content, and visual elements of the leaflet. Design software is utilized for creating digital artwork files that incorporate text, images, logos, and other graphical elements. Pre-flight checks ensure digital files meet printing specifications, while color proofing ensures accurate color reproduction before printing.
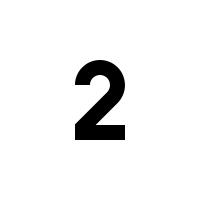
PLATE MAKING
- Transfer digital artwork onto printing plates using computer-to-plate (CTP) technology.
- Generate separate plates for each color channel (CMYK) to facilitate the offset printing process.
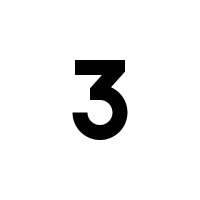
OFFSET PRINTING
- Set up the offset printing press and load the printing plates.
- Print the leaflets on large sheets of paper or cardstock using CMYK ink colors.
- Monitor print quality and make adjustments as needed to ensure consistent color and imagereproduction.
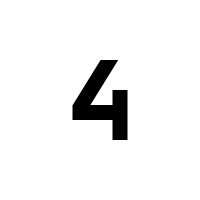
FINISHING OPTIONS
1.Coating: Apply coatings such as varnish or aqueous coating to enhance the appearance and durability of the printed leaflets.
2. Folding: Use-autoated folding machines to fold the printed sheets into the desired leaflet size and format.
3. Cutting: Trim excess paper from the edges of the folded leaflets using cutting equipment of a clean, professional finish.
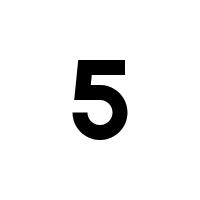
QUALITY CONTROL
1. Visual Inspection: Check printed leaflets for color accuracy, print defects, and alignment throughout the production process.
2. Folding Accuracy: Verify that folded leaflets meet size and fold specifications, with no misalignments or creasing issues.
3. Coating Consistency: Ensure that any applied coatings are evenly distributed and free from streaks or imperfections
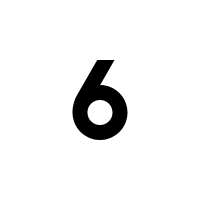
PACKAGING & DISTRIBUTION
1. Bundle and package the finished leaflets into appropriate quantities for shipping and
distribution.
2. Apply labels, bar codes, or other identifying markers as needed for inventor management and tracking.
3. Coordinate with logistics partners to arrange for timely delivery to customers or distribution
centers.
Throughout each stage of the production process, effective communication, coordination, and quality control are essential to ensure the timely delivery of high-quality offset packaging that meets the needs and expectations of clients and end-users.
In the offset packaging production process, implementing effective in-process quality contorl meares Is essential to ensure that each step meets the required standards and specifications. Here’s a breakdown of quality control checkpoints throughout the offset packaging production process
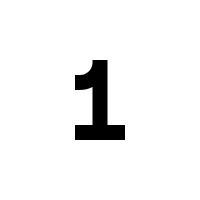
PRE-PRESS QUALITY CONTROL
- Verify digital artwork files for correct color mode
(CMYK), resolution, and appropriate bleed and trim
marks. - Conduct pre-flight checks to identify any potential issues with fonts, images, or graphics.
- Ensure accurate plate imaging and registration to prevent misalighment during printing.
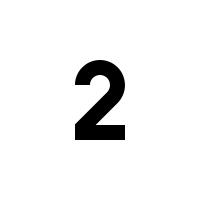
PRINTING QUALITY CONTROL
- Monitor ink density and color balance on press to achieve consistent color reproduction.
- Perform periodic checks for print defects such as streaks, smudges, or ink blotches.
- Inspect printed sheets for registration accuracy and uniform coverage across the substrate.
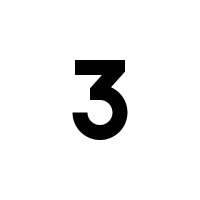
COLOR MANAGEMENT
- Use color management tools and procedures to maintain color accuracy throughout the printing process.
- Regularly calibrate printing equipments, including monitors, printers, and spectrophotometer.
- Compare color proofs with final prints to ensure consistency and adherence to color standards.
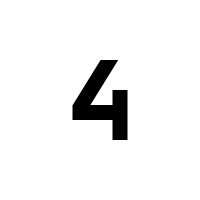
SUBSTRATE INSPECTION
- Inspect incoming cardboard and paper stock for its appearance, size, and weight so that it meets standards for quality.
- Conduct periodic checks during printing to identify any substrate defects or irregularities that may affect print quality.
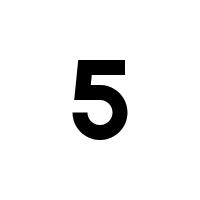
FINISHING QUALITY CONTROL
- Inspect die-cutting and creasing accuracy to ensure proper shaping and folding of packaging materials.
- Monitor coating and finishing processes to verify uniform application and adherence to specifications.
- Conduct visual inspections of finished packaging for any defects, such as scratches, scuffs, or misprints.
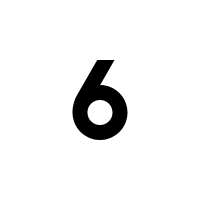
DIMENSIONAL ACCURACY
- Verify the dimensions of finished packaging products to ensure they meet design specifications and fit requirements.
- Use precision measuring tools sucha as calipers or rulers to assess accuracy and consistency.
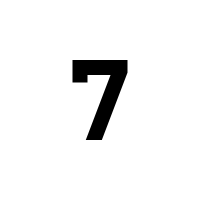
ADHESIVE & SEALING INTEGRITY
- Check adhesive application and bonding strength to
ensure secure Sealing of packaging seams and flaps. - Conduct peel and shear tests to assess the performance of adhesives under various conditions.
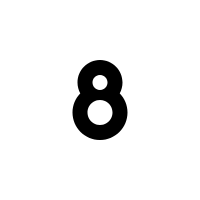
PACKAGING AND LABELING
- Ensure accurate labeling and identification of finished packaging products.
- Verify packaging quantities and configurations to match customer orders and shipping requirements.
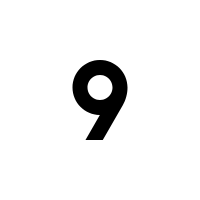
DOC & RECORD-KEEPING
- Keep complete records of all assurances of quality and checks that are carried out along the production process.
- Document any deviations from standards and corrective actions taken to address quality issues.
The Production Process Flow in cartons for offset
packaging involves several
key stages to ensure the efficient and effective creation of high-quality
packaging materials. Here's a step-by-step overview of the typical process
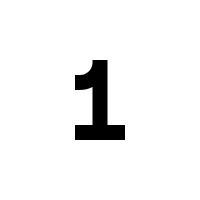
PRE-PRESS PREPARATION
- Design and artwork creation: Graphic designers
create the artwork for the packaging, considering
branding, product information, and visual appeal. - Pre-flight checks: Verify that digital files are
correctly formatted, with proper colour modes
(CMYK), resolution, and necessary bleed and
trim marks. - Plate making: Transfer digital artwork onto
printing plates using computer-to-plate (CTP)
technology, ensuring accurate reproduction of
images and text.
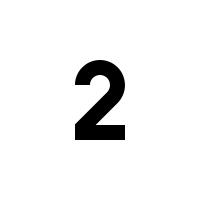
PRINTING
- Offset Printing: Use offset lithography printing
processes to transfer ink from the plates onto the
substrate (typically paperboard or cardstock) in a series of CMYK color passes. - Color Calibration: Monitor and adjust ink density, registration, and color balance to maintain consistent print quality throughout the print run.
- Specialty Finishes: Apply additional printing techniques such as varnishes, coatings, embossing, or foil stamping for enhanced visual appeal and protection.
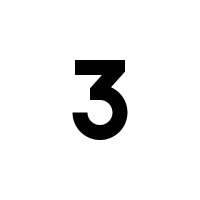
DIE CUTTING & CREASING
- Die Cutting: Use custom-designed cutting dies to precisely cut the printed sheets into individual
packaging shapes. form. - Creasing: Create score lines or creases on the packaging material to facilitate folding and assembly later in the process.
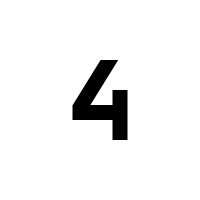
FOLDING AND GLUING
- Folding: Fold the die-cut packaging blanks along the score lines to create the desired structure and Form.
- Gluing: Apply adhesive to the appropriate areas of the packaging using automated glue application systems, ensuring secure bonding of seams and flaps.
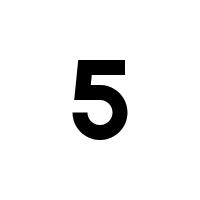
QUALITY CONTROL
- Visual Inspection: Check printed packaging for color packaging for color accuracy, print defects, and dimensional accuracy throughout the production process.
- Structural Integrity: Assess the strength,
durability, and functionality of the finished
packaging to ensure it meets design specifications
and performance requirements.
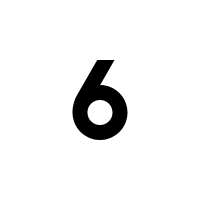
FINISHING
- Additional embellishments: Apply any additional finishing touches such as spot varnishes, embossing, debossing, or specialty coatings to enhance the appearance and tactile qualities of the packaging.
- Inspection and packaging: Conduct final quality
checks and pack the finished packaging materials into appropriate containers for shipping and distribution.
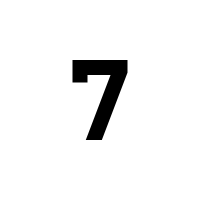
SHIPPING & DISTRIBUTION
- Packaging and Labeling: Prepare shipping containers and apply appropriate labels and markings for easy identification and tracking.
- Logistics Coordination: Coordinate with Logistics partners to arrange for timely delivery of finished packaging to customers or distribution centers.
Throughout each stage of the production process, effective communication, coordination, and quality control are essential to ensure the timely delivery of high-quality offset packaging that meets the needs and expectations of clients and end-users.
Our Infrastructure
Royal Arts operate from its new state of the art 51000 sq feet manufacturing plant, which is a marvel to witness, Royal Arts is spreaded over sprawling area of 2000 sq yards with a covered area of 51000 sq feet with the best technology avaiIable today
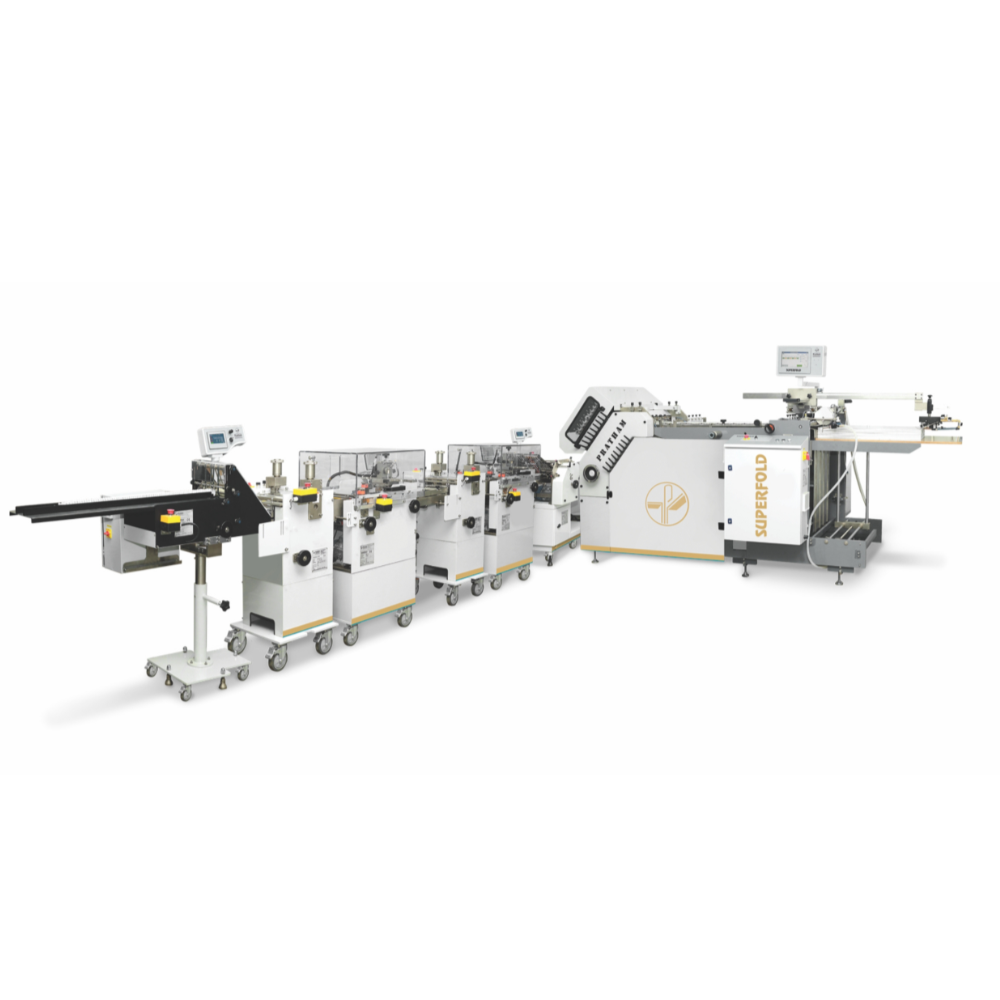
OUTSERT FOLDING MACHIN
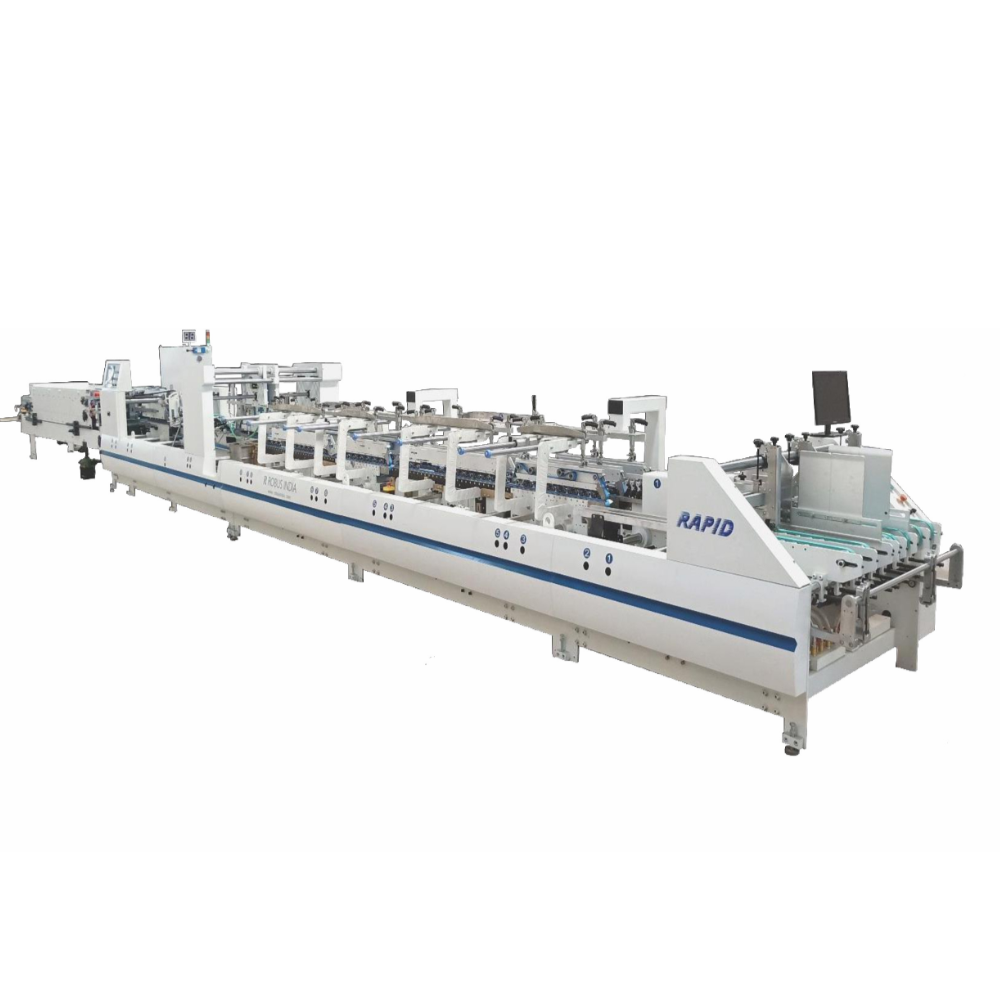
GULUR FOLDER MACHINE
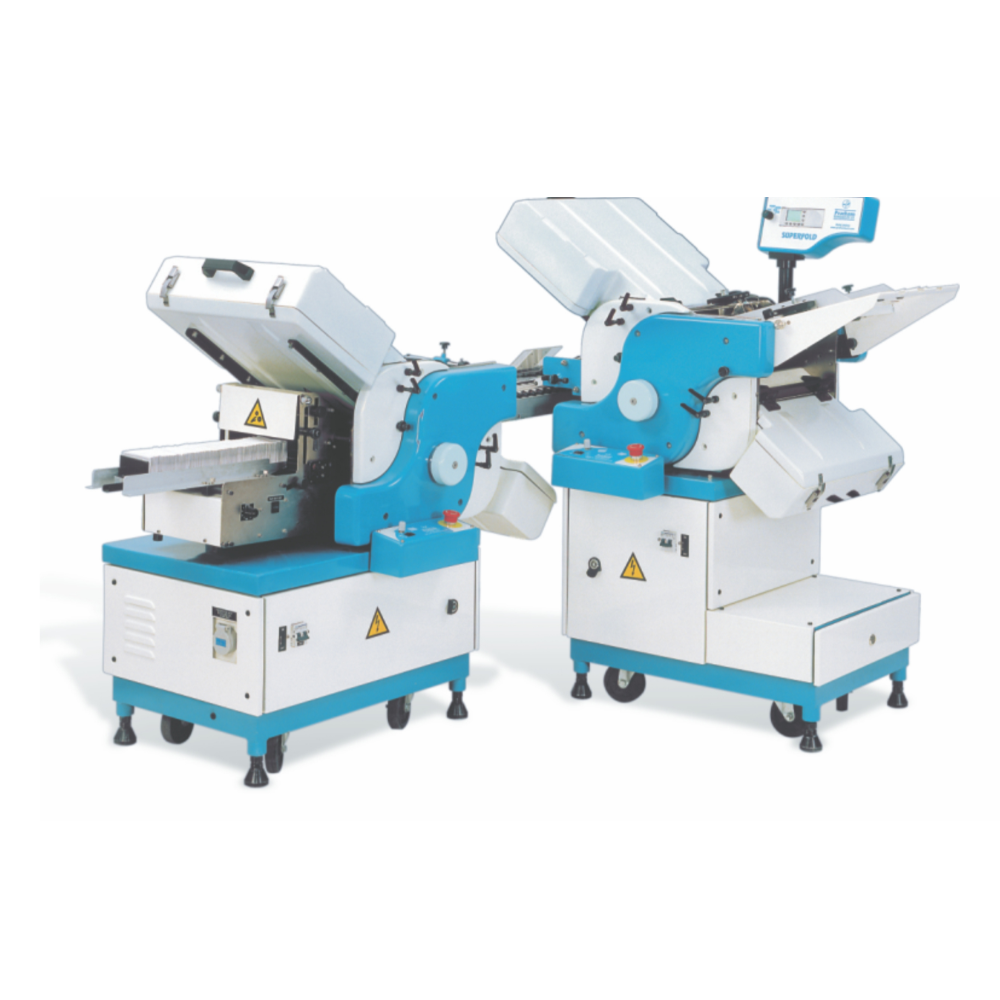
LEAFLETS INSERTS FOLDING
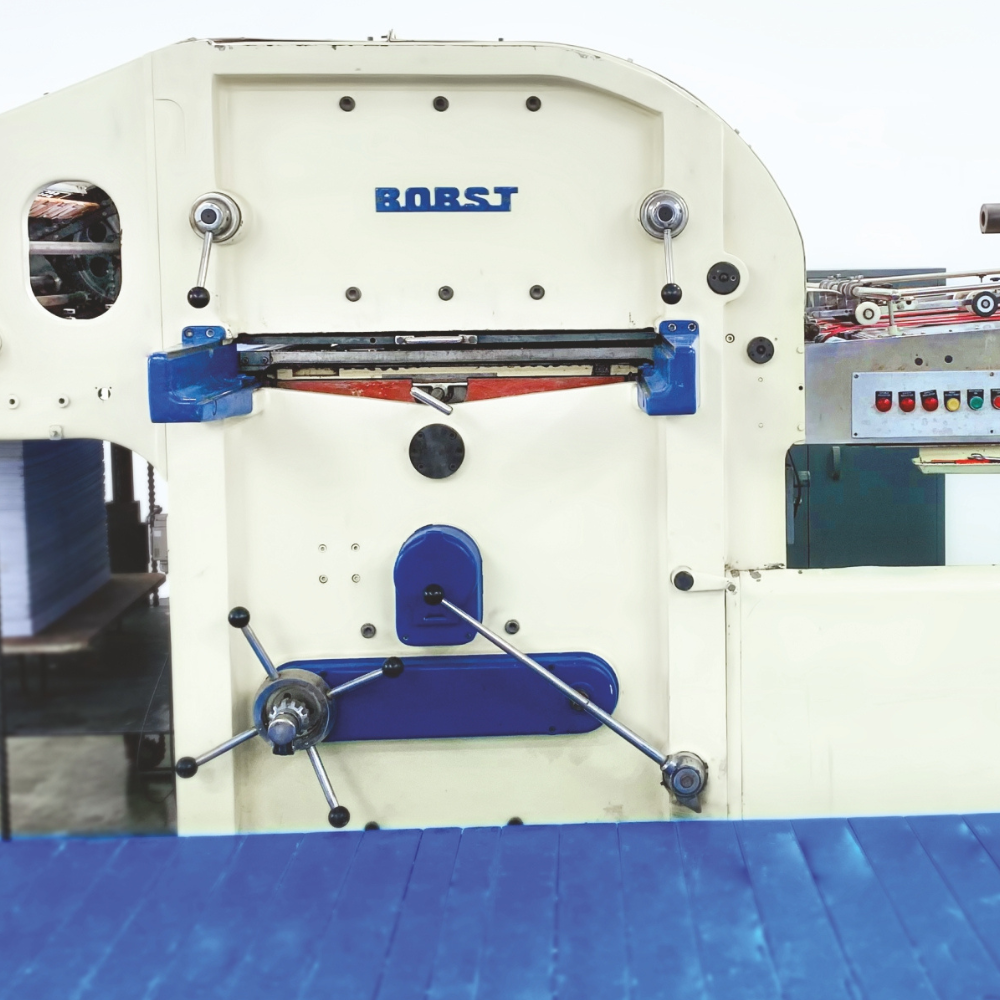
DIE CUTTING MACHINE
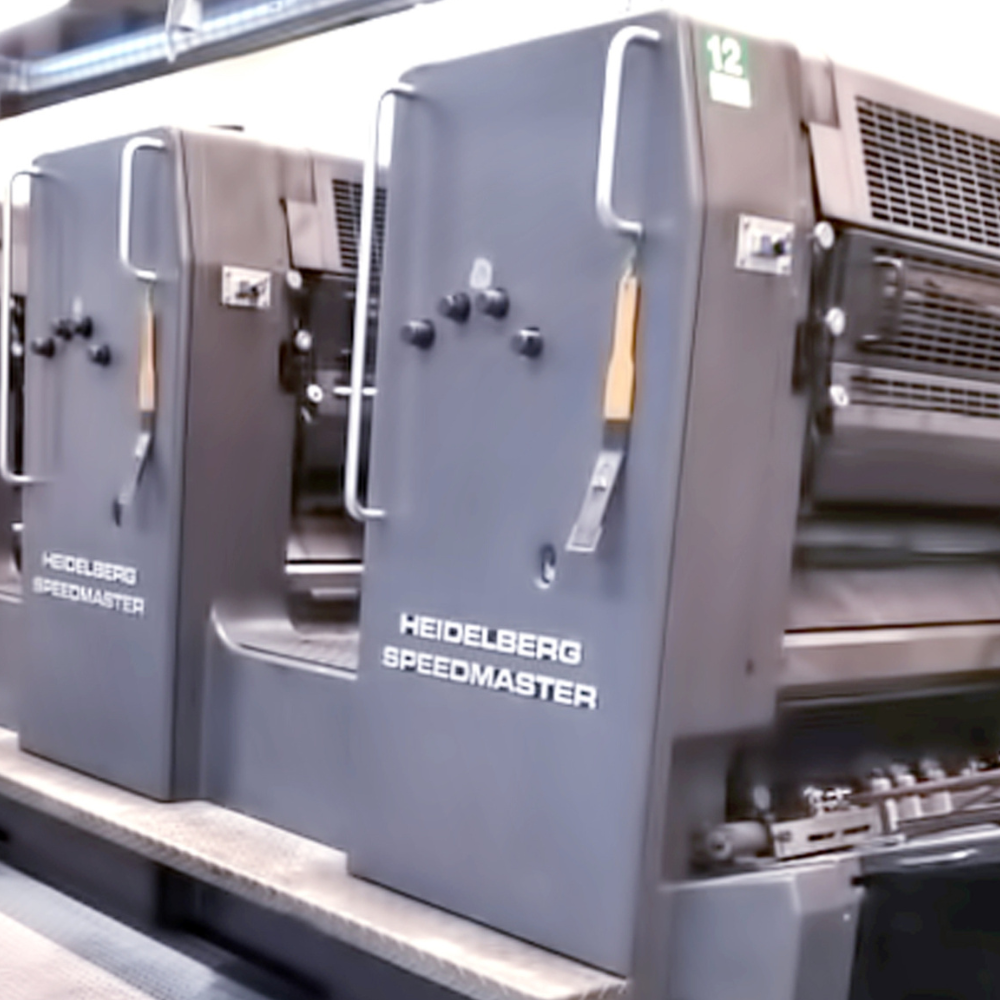
OUTSERT FOLDING MACHIN
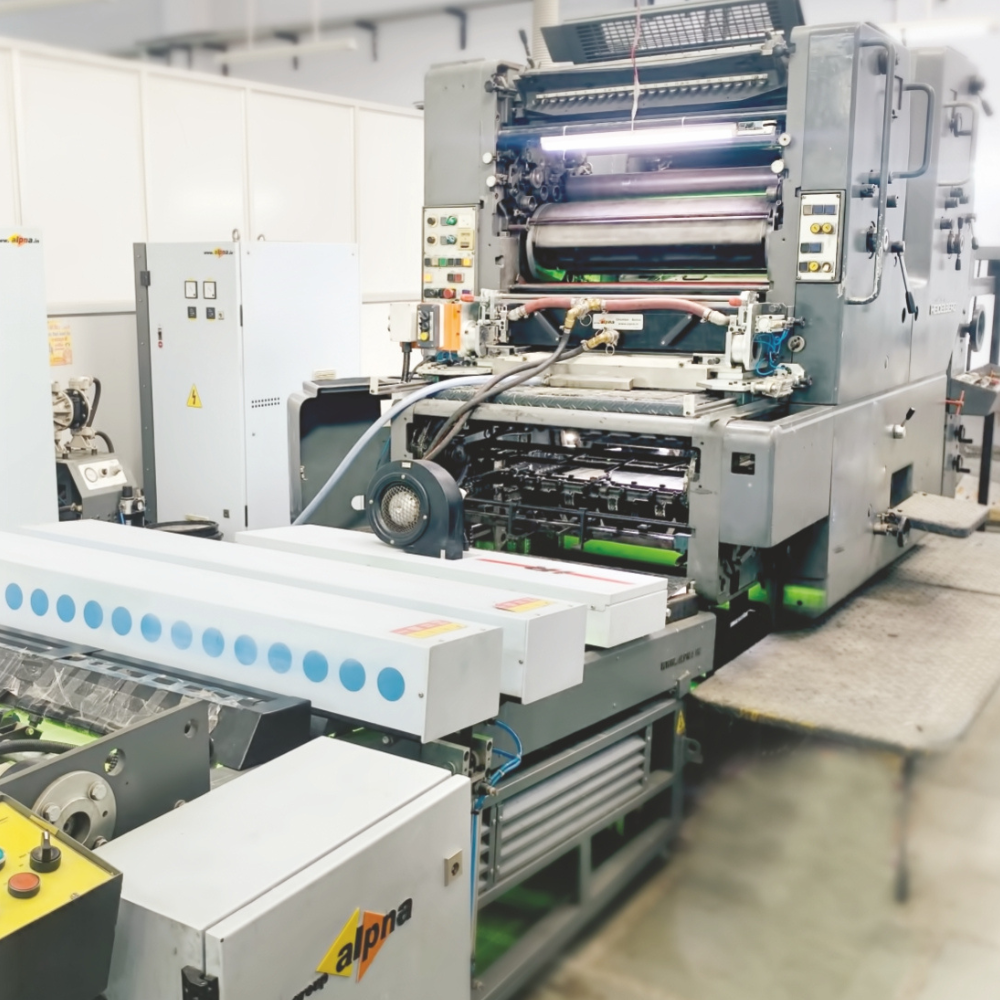
OUTSERT FOLDING MACHIN
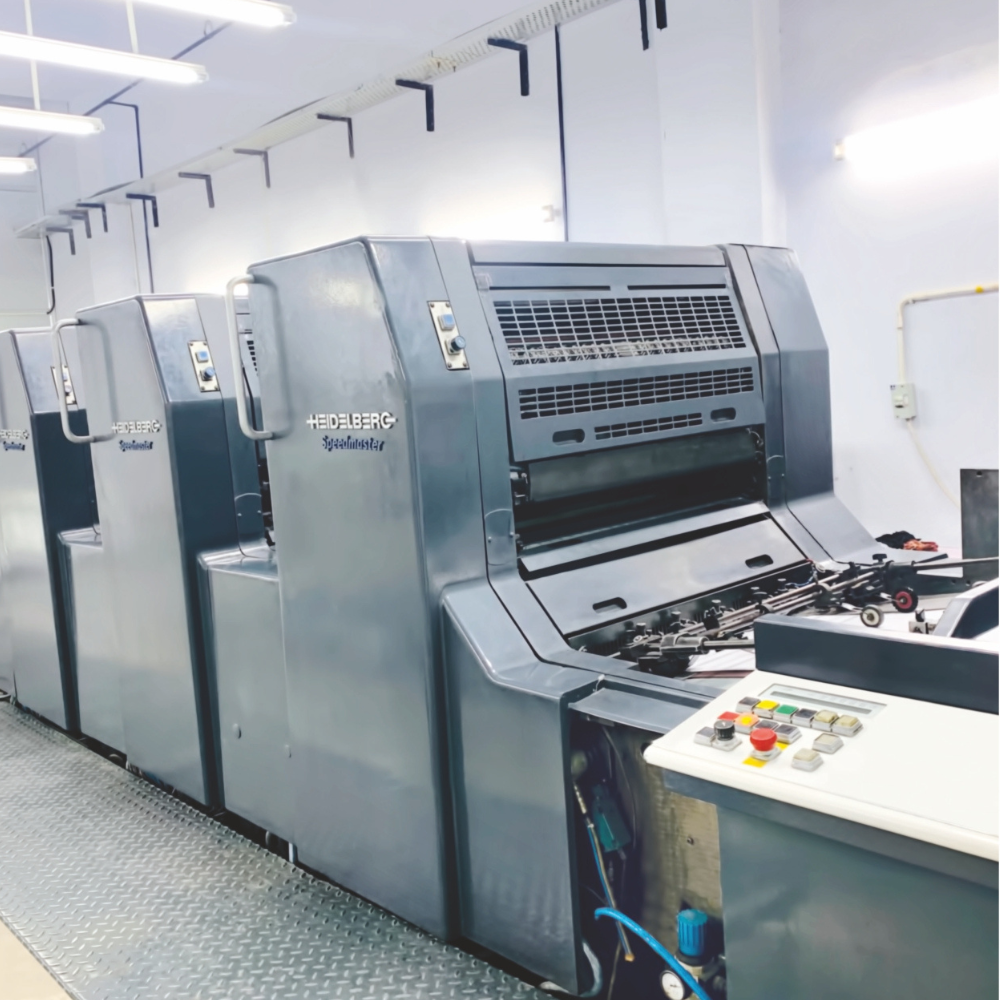
OUTSERT FOLDING MACHIN
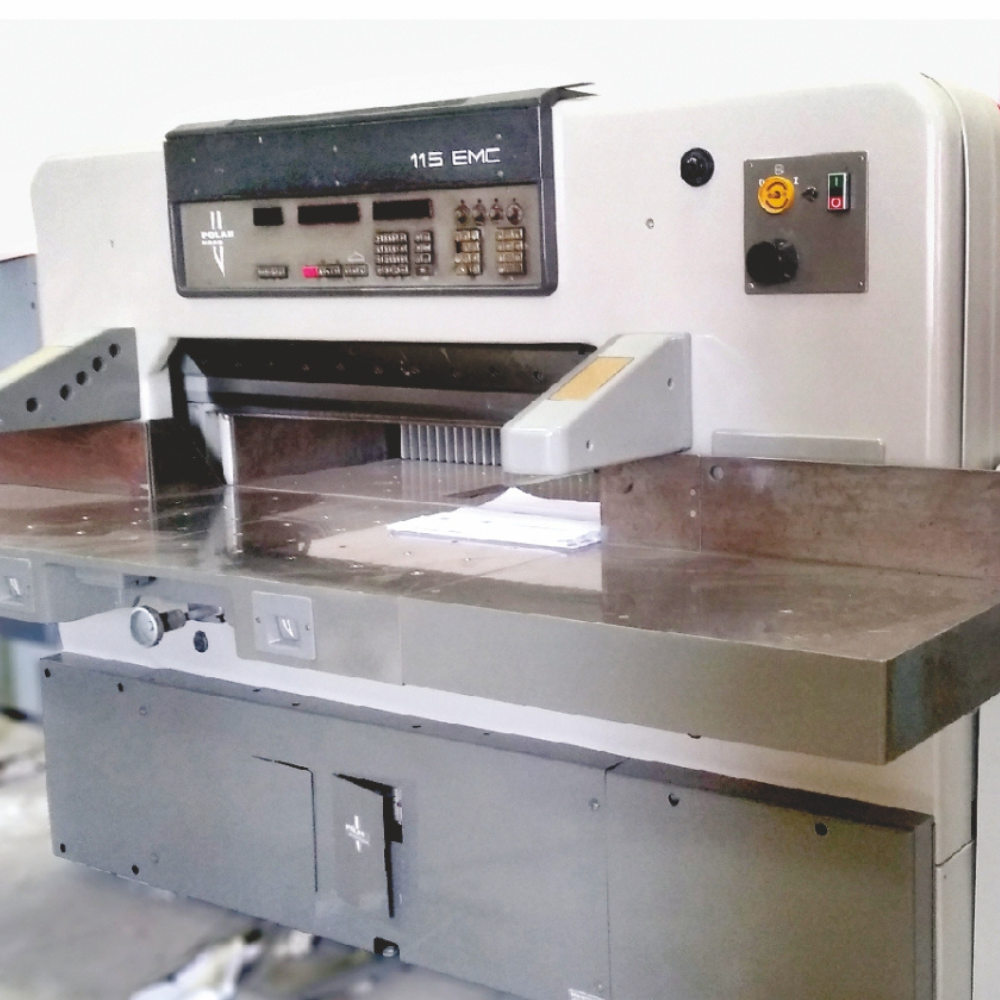
OUTSERT FOLDING MACHIN
Finest Creative & Printing Solution
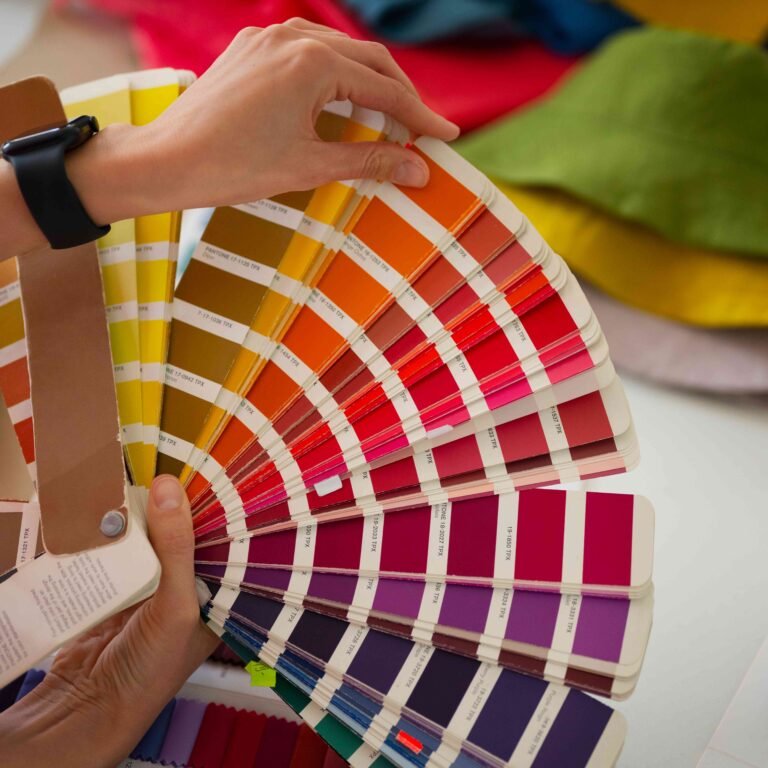
Why Choose Royal Arts
Organisational quality depends on the people or groups in charge of their responsibilities, but due to process complexity, individual control is challenging and requires teamwork or successful process improvement.
Our team is hardworking, enthusiastic, and open to new challenges. A person who is eager about what they do is more creative focused, and motivated to excellence. Ensuring the satisfaction of our clients.
Perfect time management allows us to deliver materials on schedule, prioritizing timely deliveries as our top priority. This ensures client satisfaction and helps us top client's charts when it comes to timely deliveries.